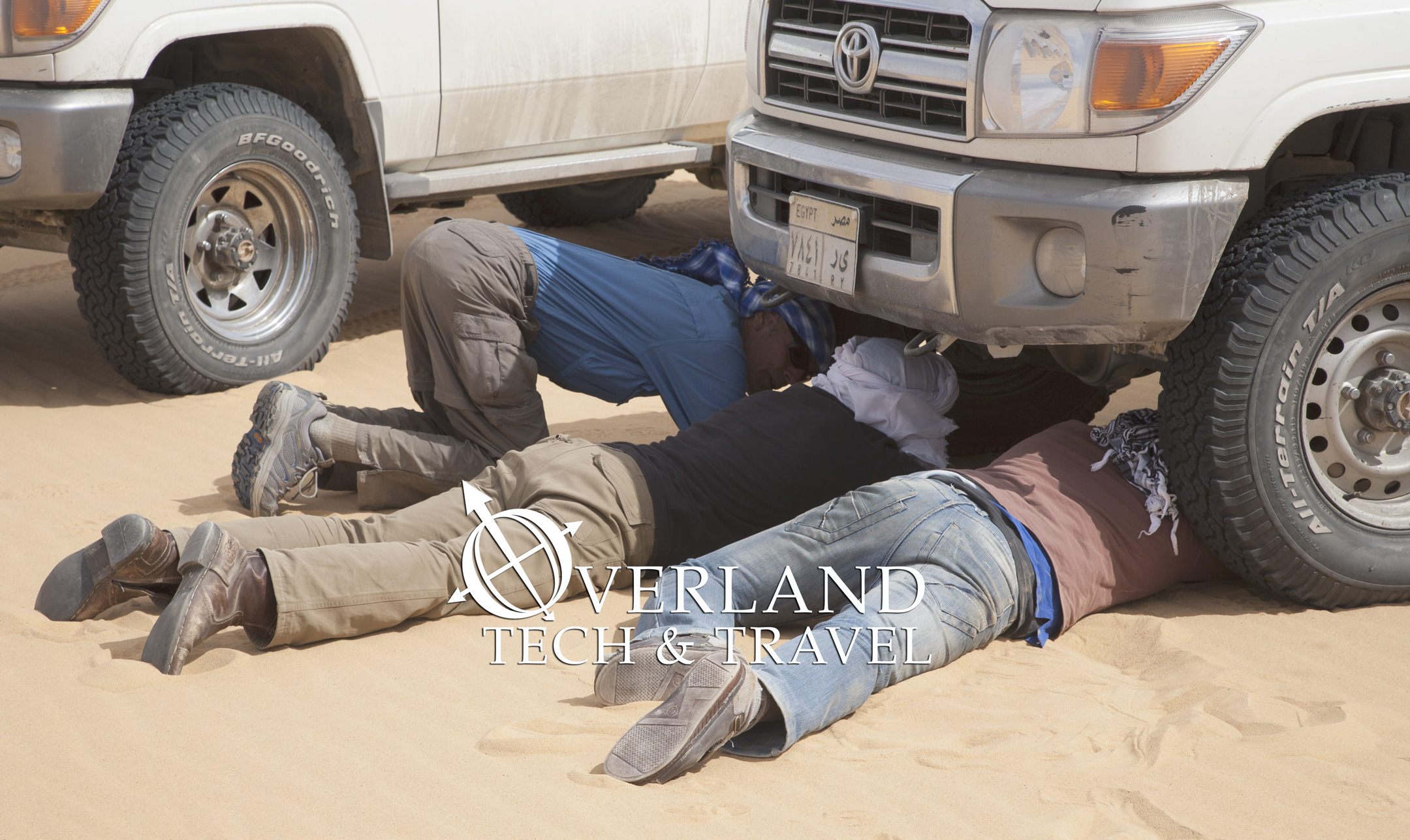
Overland Tech and Travel
Advice from the world's
most experienced overlanders
tests, reviews, opinion, and more
An odd winch bumper
I’m always on the lookout for inspiring—or horrifying—modifications and accessories on the four-wheel-drive vehicles I spot anywhere in the world. But this curious example was right here in Tucson.
I’ve written many times about the critical need to have visual and tactile access to the winch drum, and if this Jeep actually had a winch mounted to the bumper the operator would certainly have that access. But the plate securing the roller fairlead stumps me. For the life of me I cannot figure out the point of having it angled the way it is. The best wild guess I could come up with is that it vaguely mimics the look of the “stingers” so popular in a certain segment of the 4x4 community; however, it certainly wouldn’t function as one, and looks to me like it would hamper the function of the fairlead.
With no winch mounted it’s difficult to be certain, but it appears the winch line would skim the bottom of the cutout for the fairlead very closely indeed when the drum was full. Since the side rollers are angled, a side pull would result in the line partially dragging on the roller, reducing its effectiveness—a minor flaw to be sure, since given a hawse fairlead the line drags all the time. However, on a steep uphill pull (a common winching scenario) with a side pull factor thrown in, the line would be at a very steep angle near the top of the side roller.
Finally, on a general note: While I’m no welding expert, the bead along the winch plate and fairlead plate is really sloppy, and looks as though it might be lacking adequate penetration as well.
An odd winch bumper, to be sure.
Old school and new school . . .
Here's something you don't see every day: a PTO winch spooled with synthetic line.
PTO (Power Take Off) winches were common decades ago on Land Rovers and Land Cruisers. Rather than being powered by electricity, they ran off a driveshaft attached to an auxiliary gearbox on the transfer case. The advantage to them was that as long as the engine was running, the winch would run as well, with zero danger of overheating as is quite possible with the electric version. The disadvantage, of course, was that if the engine was not running, neither was the winch. These days very few vehicles are equipped with the take-off point on the transfer case that accepts the PTO driveshaft.
I had a PTO winch on my FJ40 for some time, but after I swapped transmissions I kept putting off cutting the hole in the new tunnel for the operating linkage, so the winch became nothing but a fashion item. When a Warn 8274 electric winch presented itself as the perk from a review, I swapped that in and sold the PTO for four times what I'd paid for it.
Probably a mistake—one Maggie McDermut did not make with her BJ74 Land Cruiser. At the 2018 Overland Expo West, the lads from 7P Overland spooled 80 feet of 3/8ths-inch Dyneema onto the drum, and spliced in a Factor 55 thimble. She now has the best of old and new.
The drive mechanisms on PTO winches varied from year to year and maker to maker. Maggie's is perhaps ideal, in that the winch can be run in any gear, depending on the speed and power needed. Choose first gear for low speed and high power, or run it in second or even third with more throttle if you're just pulling a small log off the road. The single disadvantage of her setup as it is now is the hawse fairlead, which is inset into the chrome front bumper, and could very well let the line contact the edges of the opening on either a right or left-side off-center pull. She'll need to use caution to arrange a straight pull.
I hope she gets a chance to use it on her journey to Alaska as a Change Your World Fund grantee.
So much wrong here
I copied this photo from the excellent American Adventurist site, where it was posted as an example of how not to rig a winch.
Indeed. Yet this is not some low-budget bodge job on a winch installation. There are quality products represented here—a Warn winch and synthetic line. But several things set off alarms.
Let's begin with the least-egregious aspect: that winch hook stuffed into the recovery loop. There is nothing wrong with the standard open winch hook, although aside from being quicker to deploy it suffers when compared to a closed thimble, which is positively connected to the winch point with a shackle and cannot come loose inadvertently. What worries me here is that the spring-loaded safety tab could easily be stressed and bent the way it is forced open, possibly interfering with its effectiveness or even damaging it.
Next there is the hawse fairlead. As with the hook, there is nothing wrong with a hawse fairlead, although it is a myth that you should use only a hawse fairlead when running synthetic winch line. A roller fairlead is fine for synthetic line and is in fact easier on the line. The problem with this particular hawse fairlead is the extremely shallow chamfer on the opening, which will severely stress the line when used on an off-angle pull. The chamfer on such a fairlead should ideally have a radius six times the radius of the line itself. Here is a much better hawse fairlead:
The real disaster here, however, is the line, which is spooled over the top of the drum rather than under the bottom. Besides causing the remote to work backwards—"in" will spool out and vice versa—and the fact that the line has a much more acute angle to travel through the fairlead, there are two genuinely dangerous results. First, pulling in line over the top of the drum on a winch mounted this way, with the feet down, moves the center of force farther away from the mount, increasing the stress on it. Second, the brake will not operate correctly if, for example, the operator needs to lower a vehicle down a steep incline, although Warn tells me the winch will still not let the vehicle free-fall.
A vehicle-mounted winch is not a tool to be installed casually or carelessly. I worry that the person to whom this one belongs will have taken the same approach to learning how to actually use it. Not a good scenario.
A challenge to winch bumper manufacturers
Once upon a time, adding a winch to an overland vehicle was easy. Series 2 and 3 Land Rovers, 40-Series Land Cruisers, and Jeeps were built with chassis rails that extended a good foot in front of the radiator, fronted by a solid steel bumper. To mount a winch you basically plopped it there, bolted it down, and hooked up either a PTO driveshaft or wiring. Done. Even the bulky Warn 8274 on my FJ40 was an easy installation.
It’s different these days. With scant few exceptions, those protruding steel bumpers have been sacrificed in the (commendable) search for aerodynamics—i.e. fuel economy—and safety, via computer-designed crush zones and air bags. Give me a choice of being in the 40 or our Tacoma in a head-on collision and there’s no doubt which I’d choose.
But if you want to install a winch on these new vehicles, you need to replace the 10-pound body-colored plastic facade that looks like a bumper with a dedicated steel or aluminum structure properly connected to the chassis of the truck, and capable of absorbing several tons of force. Thankfully, numerous companies have risen to the challenge, especially for the more popular models of pickup and SUV.
However—I seem to be noticing a trend in aftermarket winch bumpers that is vaguely unsettling: a trend toward fashion over function. That 8274 on my FJ40 is right out in the open—I can see it operating, I can watch to make sure the line is spooling correctly, and if it isn’t I can stop the procedure and fix it. One of the requirements to pass the winching section in the N.P.T.C. Certificate of Competence in 4WD is, “Ensure the winch components are in suitable condition.” Another is, “Ensure the winch is free from obstruction and the line is spooled properly.” Both are easy to confirm with that 8274.
With an increasing number of modern winch bumpers, either is virtually impossible. The only view of either the winch or the drum and line is a peek through the fairlead. A tiny hole gives you access to the engagement lever. Recently I was respooling line on a student’s winch and had to have him shine a flashlight through the fairlead while I crouched in front of it and peered inside so I could ensure the line was going in correctly. Had there been a bad snarl we would literally have had to remove the bumper to fix it.
Anther vital winch-bumper component is either shrinking or going away altogether—recovery points capable of and suitable for attaching a shackle. Properly, a shackle eye should be nearly as thick as the width of the jaw on a shackle, to prevent twisting and off-angle stresses. Lately I’m seeing them much narrower—or simply missing, so that there is no provided way to rig a double-line pull from your winch to an anchor point and back to your bumper, or to safely secure a friend’s winch line to your vehicle.
Several months ago I spoke to a rep from a major bumper manufacturer (I’m not going to name names in this piece because I’m not discussing quality, which is uniformly high in this segment; I’m discussing choices made by the manufacturer and consumer). The rep said that recovery points had been eliminated on his company’s bumpers due to airbag compatibility issues. I’m . . . not sure about this. It’s my understanding that airbags are triggered by accelerometers, which detect deceleration consistent with that of a collision severe enough to warrant deployment, and then send a trigger signal to the device. Often these accelerometers are positioned in the cab of the vehicle, nowhere near the bumper. In any case, if you make a bumper capable of withstanding several tons of pull provided by the winch mounted on it without affecting airbag deployment, I can’t understand why adding recovery points capable of withstanding several tons of pull would suddenly compromise the system. (Note that I did not say it can’t be so; I simply said I don’t understand how it could be so.)
One source I spoke to told me that the only thing separating airbag-compliant winch bumpers from non-airbag-compliant winch bumpers is that the maker of the latter did not spend the huge amount of money necessary to actually conduct crash tests to prove unequivocally that the vehicle’s airbag will still deploy with the bumper mounted. In researching various crash reports I have yet to come across a case in which it was proven that an aftermarket bumper prevented an airbag from deploying (if anyone reading this has such documentation I’d be grateful to hear about it).
The only potential effect of a winch bumper on airbag deployment that I know of is the risk of triggering in a collision that occurs at a lower speed than that at which the accelerometer would normally trigger the device. Some vehicles are built with crush cans behind the stock bumper, designed to absorb the energy in a minor collision without setting off the airbag. An aftermarket bumper that eliminated these crush cans and tied directly to the frame could potentially fool the carefully calibrated sensors into “thinking” that the crash was worse than it actually was. This would certainly be an alarming (and probably expensive) surprise, but one unlikely to cause serious injury.
I’d like to see—within the boundaries of passenger protection in a collision, of course—a return to winch bumpers that optimize access and safety for the winch operator. Winching is an activity fraught with potential risks at the best of times; deliberately making it difficult or impossible to ensure the winch is operating correctly is a big mistake. At the very least, a bumper should be equipped with a removable access port that allows full-width access to the drum and line. And the bumper needs to be equipped with proper recovery points that will adequately support a shackle—either that or the manufacturer could offer separate, frame-mounted recovery points.
There’s nothing wrong with fashion, as long as it does not compromise function. The best functional designs make their own fashion—what can be better looking than something that works perfectly?
Hint: When using “Search,” if nothing comes up, reload the page, this usually works. Also, our “Comment” button is on strike thanks to Squarespace, which is proving to be difficult to use! Please email me with comments!
Overland Tech & Travel brings you in-depth overland equipment tests, reviews, news, travel tips, & stories from the best overlanding experts on the planet. Follow or subscribe (below) to keep up to date.
Have a question for Jonathan? Send him an email [click here].
SUBSCRIBE
CLICK HERE to subscribe to Jonathan’s email list; we send once or twice a month, usually Sunday morning for your weekend reading pleasure.
Overland Tech and Travel is curated by Jonathan Hanson, co-founder and former co-owner of the Overland Expo. Jonathan segued from a misspent youth almost directly into a misspent adulthood, cleverly sidestepping any chance of a normal career track or a secure retirement by becoming a freelance writer, working for Outside, National Geographic Adventure, and nearly two dozen other publications. He co-founded Overland Journal in 2007 and was its executive editor until 2011, when he left and sold his shares in the company. His travels encompass explorations on land and sea on six continents, by foot, bicycle, sea kayak, motorcycle, and four-wheel-drive vehicle. He has published a dozen books, several with his wife, Roseann Hanson, gaining several obscure non-cash awards along the way, and is the co-author of the fourth edition of Tom Sheppard's overlanding bible, the Vehicle-dependent Expedition Guide.