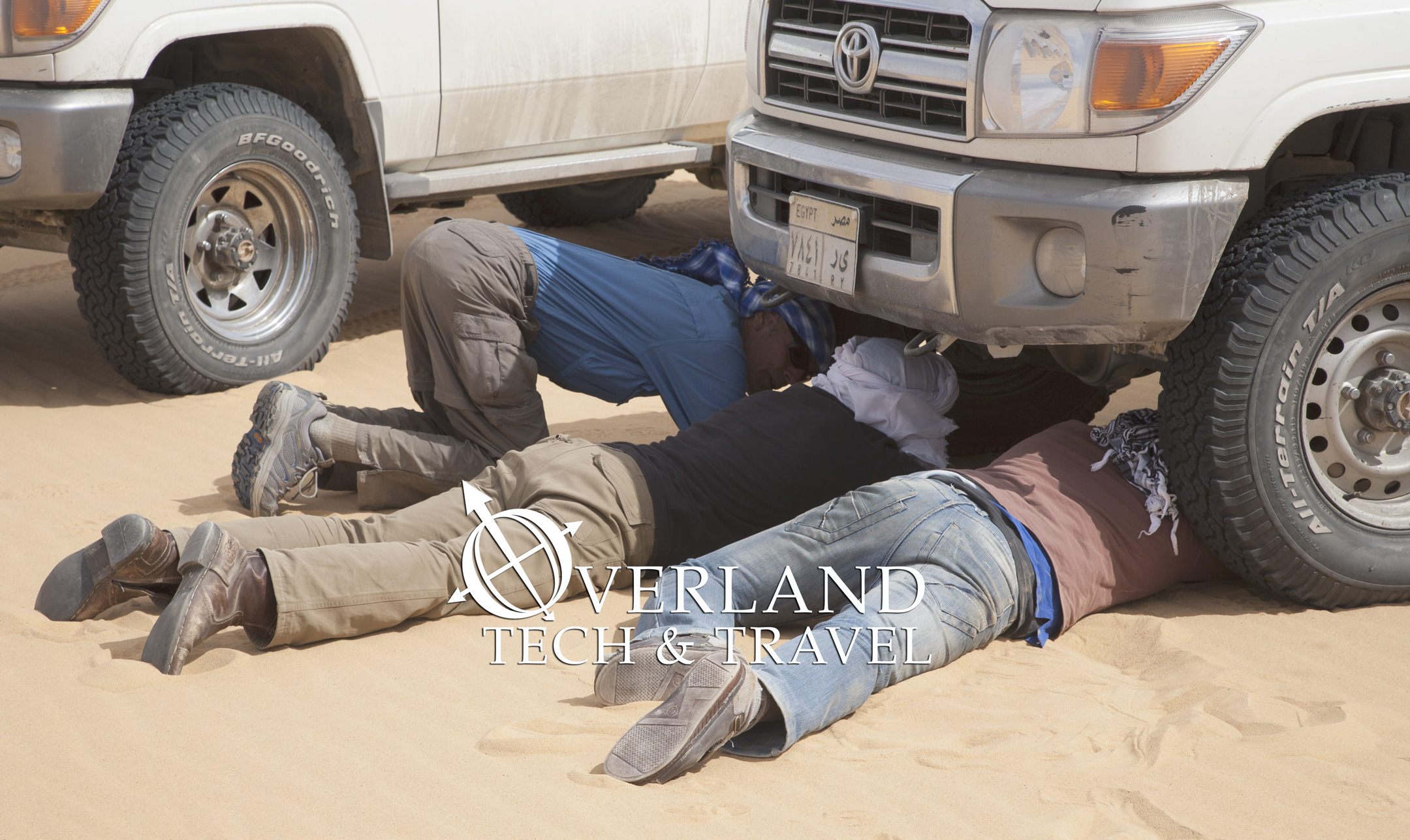
Overland Tech and Travel
Advice from the world's
most experienced overlanders
tests, reviews, opinion, and more
Bringing back the spirit: Exploration Quarterly Field Camps
Fifteen years later we still get these emails.
“The Overland Expo is great, but we miss the first ones!”
“The Expo is still fun, but the camaraderie isn’t there any more.”
“Lots more stuff to look at and buy, but less community spirit.”
Of course Roseann and I were thrilled—and more than a bit stunned—at the success of the event she started in 2009. In fact it eventually became just too big for her to manage, and its very success hindered our own travels, which was not the plan . . .
Now we are back to our roots in journalism, field arts, exploration, and conservation with the debut of Exploration Quarterly, which encapsulates all our passions.
And yet, we still miss those first few Overland Expos too, and our original family—both the attendees who still write us and our core team: Graham Jackson, the Camel Trophy team members, the vendors who took a chance on us.
So we’ve decided to bring that spirit with the Exploration Quarterly Field Camps. Our first will be held in one of our favorite spots, the private Aravaipa Canyon Ranch. The group will be limited to a maximum of 45—thus making even the first Expo seem big. Our activities are going to span a range including skills clinics, equipment demonstrations and samples, vehicle topics including driving and recovery (the ranch has miles of private roads), natural-history hikes, and campfire happy hours. Our director of training for the Expo, Graham Jackson, will be there, as will Camel Trophy veteran Jim West, who is well-known to double as a stand-up comedian. We’re looking for old friends and new to join us. The signup link is right here.
I’ll have lots of equipment on hand to try—for example a Freedom Recovery becket kit to rig a three-to-one winch system:
Also an interesting new compact wall tent from White Duck:
And many other new products. There are sure to be many cool vehicles.
Given the beautiful location, we’ll be keeping a Swarovski spotting scope trained on the cliffs to look for bighorn sheep (and, later, planets). And you never know what other wildlife we might find.
We still have spots left. Please join Roseann and me for the start of a new tradition!
Do-it-yourself alignment with the Gyraline
Ever since we bought our 2014 Tundra, it has exhibited a slight pull to the right, despite the fact that the used-car dealer from whom we bought it claimed to have performed an alignment. Taking it in to a professional alignment shop was one of those tasks that are just so easy to put off—like for three years?
A few months ago I installed a complete parabolic suspension on our FJ40. After such a swap it’s smart to have an alignment done. Especially important is checking for caster, which will change with a suspension lift on a solid-axle vehicle and can significantly affect handling. (Caster is the near-but-not-quite vertical axis around which the front wheels turn.) Now I had two vehicles that needed an alignment. And now I was looking at around $250-$300 plus the time (x2) out of my day to have them both done.
Finally . . . right now I have another parabolic suspension kit waiting to be installed on the Troop Carrier. So yet another alignment, another day lost, and another $125-$150 minimum. Ugh.
Then I got an email from friend and master Toyota mechanic Bill Lee, about this tool.
The Gyraline comprises a deceptively simple plastic plate, apparently 3D printed, with a clamp that allows you to secure an iPhone (or Android) to it. The magic part of the device is all in the software, which guides you step by step in measuring—with the accuracy of a professional alignment rack—all aspects of a vehicle’s alignment on all four wheels: toe, camber, caster, even Ackerman angle.
Once the app is loaded you simply follow prompts to place the device against each wheel, level it using the central green diamond, the tapping the relevant wheel. Move to the other side and repeat, and you’ll have your toe-in or toe-out to a fraction of a degree. Thirty seconds max. Other measurements are nearly as simple.
I was so impressed that I intended to write an in-depth article, but honestly the thing is so easy to use there’s just not much more to say. The Gyraline is not only useful for general alignment but also when doing such jobs as replacing tie rod ends. Most enthusiastically recommended.
Canyon Cooler versus Oyster Tempo cooler: Premium ice chest versus super-premium ice chest.
We were early and enthusiastic adopters of the portable 12V fridge concept—first with the classic and dependable Engel, later a series of ARB models, and a superb National Luna model that rides permanently in our 70-series Troop Carrier. I wouldn’t want to travel without one, and I’d certainly never go back to the giant Coleman ice chests and the inevitable three-day slurry in the bottom as 20 pounds of ice melts its way into everything not hermetically sealed.
Day trips and picnics are a different matter. Then it’s nice to have a compact cold-box you can easily carry away from the vehicle, just large enough to hold lunch and drinks. However, most inexpensive ice chests I’ve seen are of terrible build quality and low efficiency—inevitably a throw-away item once the thin plastic shell cracks and the rigid foam deteriorates. We’d generally find at least one or two in the dumpsters after every Overland Expo, destined for a landfill or worse. (Obviously, the less said about the $10 styrofoam grocery-store versions, the better.)
A couple of years ago Roseann bought a 22-quart ice chest from Canyon Coolers, an Arizona company that got its start making rugged super-sized ice chests for river runners. And this mini-me version is indeed rugged, made from rotomolded plastic, with significantly thicker insulation than a standard Coleman-style cooler. It incorporates aluminum tie-down bars (those on the newer V2 version are molded into the plastic), a carry strap with a rubber shoulder pad, rubber feet, and a screw-in drain plug. The lid incorporates a thick rubber gasket and two strong, if somewhat fiddly latches. The price was on the high side at $150, or $170 with a fitted cold pack. (This cooler is made in the U.S.; Canyon’s larger coolers are molded in Taiwan.)
Stout doesn’t begin to describe the sturdiness of the Canyon Cooler. Not only can I stand on it, I can jump up and down on it with impunity. If you owned four of these things you could probably employ them as jack stands. Canyon Coolers offers a lifetime warranty that shows their confidence in the quality. And we found it efficient as well; although I never ran a test against a cheap cooler we both remarked on how long contents remained cold. Roseann used it on a 3,000-miles working field arts trip through five states, and only had to add a Big-Gulp-sized container of ice every two to three days to keep her milk, salads, and water cool.
Despite the cooler’s sturdiness, however, I was still a bit reticent about the plastic construction. Strong, yes—but if you ever do manage to destroy it it’s completely non-recyclable. And its very thickness and bulk would make a big chunk in a landfill.
Then, last year, I got a chance to try a whole new concept in a compact ice chest: the Oyster Tempo cooler. Manufactured in Norway from aluminum, and thus of course fully recyclable, it also incorporates a vacuum insulation system, like a Thermos bottle. The company claimed this provided cold retention superior to any standard ice chest design while reducing the volume needed for the insulation.
The Oyster cooler is certainly the most elegant ice chest I’ve ever seen, with a brushed gray finish and gently fluted sides and top. The latches and hardware are user-serviceable without tools; the lid removes completely, or you can leave the back latched and the lid will hinge up and stay open (although if you push too far the back latch will pop open). The sealing surface of the lid is over an inch wide and incorporates a rubber as well as a foil seal. The Oyster felt nearly as sturdy as the Canyon; bouncing on top felt completely secure.
The Oyster comes in a bundle that includes both a rigid swiveling handle and a soft carry strap, as well as a pair of form-fitted cold packs that cover the inside bottom, and a cloth carrying/protective bag. It’s definitely a premium package—and it comes with the premium price tag of $495, three times that of the Canyon Cooler. The earth-friendly bonafides are a given; does the performance justify the rest of the price difference?
I first measured the weight, then the outside dimensions of each chest—i.e. the volume it takes up in the vehicle—and compared that with the interior volume.
Canyon: 13.55 lbs; exterior volume: 3,325 cubic inches; interior: 1,382 cubic inches.
Oyster: 12.15 lbs; exterior volume 2,731 cubic inches; interior: 1,472 cubic inches.
So, in addition to being 1.4 pounds lighter than the Canyon, and taking up 20 percent less volume in the vehicle, the Oyster has 90 cubic inches more interior volume, thus fully justifying that part of the manufacturer’s claims.
But what about actual insulating ability? I decided to test it by putting a one-liter Nalgene with 900 ml of completely frozen water inside each chest, and measuring how much melt there was after 24 hours. This put the Oyster at somewhat of a disadvantage due to its greater interior volume, but I decided to try it anyway without any sort of a handicap. Both chests were at ambient temperature when I started, both were left on the porch through a mild spring day and overnight.
The next morning I poured off 650 milliliters of melted water from the Nalgene in the Canyon Cooler—and just 500 milliliters from the bottle in the Oyster. Especially considering the Oyster’s volume “disadvantage” for this test, it resoundingly justified the maker’s claims of superior insulating capability, even compared to another high-end cooler. We’ve confirmed this by several seat-of-the-pants tests on day trips using the fitted cold packs, remarking each time how seriously cold the contents stayed. Perhaps the Oyster should be referred to as a “super-premium” cooler.
650 milliliters melted in the Canyon Cooler
500 milliliters melted in the Oyster
Okay: the Oyster is better than the Canyon in every measurable aspect. Is it worth three times the price?
That’s going to be a highly personal decision. These are both excellent ice chests, and both should prove extremely durable. For me, the aluminum sustainability of the Oyster is a very powerful draw. The elegant style is just a bonus. I know this cooler is going to last the rest of my life and beyond; various scratches and dents will only add up to patina. And its efficiency is astonishing. The fitted cold packs completely eliminate the need for ice—I pulled a Coke out of ours on the afternoon of a 90-degree day and it was still refrigerator chilled. A super-premium cooler indeed.
First Exploration Quarterly Field Camp – April 5-8, 2025
First Exploration Quarterly Field Camp – Arizona, USA – April 5–8, 2025 at the beautiful and private Aravaipa Canyon Ranch.
Registration is open. Space will be limited.
Enjoy camaraderie with a small group of fellow overlanders, explorers, naturalists, and outdoor enthusiasts
Sunday dinner and drinks, with live music
EQ writers and photographers panels (Q&A)
Enjoy quality time with other explorers around campfires and cocktail hours; have fun with scheduled cook-offs and camp “home tours”
View and test gear up-close with Sponsors
Mini skills clinics every day: overlanding, field arts, victualling, equipment setup and use—the topics are nearly endless.
Pricing begins at just $395
For details and pricing, view our events shop.
LifeStraw’s magic little device
Growing up in southern Arizona, I learned very early on how vital water is in the desert. When my friend Bruce and I first began hiking up into the Catalina Mountains, neither of us yet eight years old, we carried ours in surplus metal GI canteens, which along with their canvas covers and three-inch-wide M36 belts probably weighed as much as the water inside. I remember distinctly the one time we miscalculated when trying a “short cut” summer climb over a ridge separating Sabino and Bear canyons. We sucked the last drops out of our canteens before we even reached the crest, and by the time we made it to the picnic area in Sabino and its taps we were pretty severely dehydrated. Never again did I hike anywhere, any time, without a generous supply of water.
Until last fall.
Roseann and I camped near the headwaters of the Little Colorado River, where I wanted to try to catch one of Arizona’s native fish, the Apache trout. This high up in its watershed the Little Colorado is small enough to jump across in places, but although its flow is year-round, drinking is not advisable due in part to the cattle grazing in the area—a possible source of Giardia.
However, I had with me one of Lifestraw’s clever filtration straws, which removes 99.999 percent of parasites such as Giardia and Cryptosporidium, 99.9999 percent of bacteria, and also microplastics. So I left the Nalgenes at the truck for a full day of fishing, carrying only the 1.8-ounce, stainless-steel filter (3.1 with carrying case). Whenever I needed a drink I simply knelt down and sipped through the straw right from the stream. It was cool to rehydrate directly (well-almost) from the Little Colorado River itself, and saved at least six pounds in my rucksack. The filtration matrix is good for about 1,000 liters, which, assuming I would have carried three liters of water otherwise, corresponds to roughly 330 such outings.
There’s nothing to using the straw except the need to use care to avoid cross-contamination. It takes a bit of effort to draw water through the filtration system, but less than I would have guessed. I finished the day a convert. I’ll carry this whenever I’m in an area with water sources that might be risky (which, according to the EPA, includes about half of all surface water in the country). And It will ride in my vehicle as a fail-safe, lightweight survival tool. Well-recommended—and, at $35, an absurd bargain.
Should you avoid buying a new Tacoma?
People love drama.
Even when it’s not real.
Owners of vehicles made by manufacturers that compete with Toyota especially love drama if it involves reliability issues with Toyotas. I remember when some first-generation Tacomas developed issues with leaking head gaskets. The howls among Ford, Chevy, and, especially, Land Rover owners reached shrill octaves: “SEE? SEE?” Ironically, the fact that Toyota’s reputation for building dependable vehicles is based on rock-solid real-world evidence is what makes any hairline crack in its armor take on the appearance of a magnitude 7.1 earthquake.
Recently the scenario has been playing out again with the news that some eight-speed Aisin transmissions in the new Tacoma have been failing—shifting poorly or becoming stuck in one gear, even suddenly shifting into neutral. Only now this drama has been amplified by several orders of magnitude thanks to the presence of numerous YouTube “experts” who know they’ll get a lot more clicks with a video shouting, “NEW TACOMA TRANSMISSION DISASTER!” or, “DON’T BUY A NEW TACOMA!” than they will with a more rational approach. Several friends contemplating purchase emailed me wondering if they should jump ship.
The issue is a real one, caused, apparently, by a faulty pressure-control solenoid. On the vehicles affected (often indicated only by several particular fault codes when the engine warning light comes on), Toyota replaces the entire transmission. But what are the chances of getting a faulty unit?
I did a bit of elementary statistical research, helped by the more level-headed YouTube authorities such as Tim Esterdahl. It turns out that, among the 192,000 2024 Tacomas sold, fewer than 1,000 have been affected by the TSB (Technical Service Bulletin). That’s about one half of one percent. (And we can assume a correction has been implemented in the production line.) Enough to spark glee among Ranger and Colorado owners, certainly, but enough to make me warn you against buying a new Tacoma? Not even close.
A Rolls-Royce . . . mouse house?
The tiny hazel dormouse (Muscardinus avellanarius) is England’s only native dormouse. Just three inches long and under an ounce in weight, it used to be common, especially in southern England, in forests with a dense understory of hazel, ivy, and honeysuckle, which allows the mice to climb into the thickets to nest in safety.
But the population of hazel dormice has plummeted in recent years, mainly through the loss and fragmentation of woodland and hedgerows.
One possible habitat for them is the enormous woodland adjacent to the Goodwood Estate and motorsports park—which itself is adjacent to the headquarters of Rolls-Royce Motorcars. To investigate the possibility of a resident hazel dormouse community, apprentices at Rolls-Royce, with input from the estate’s forestry managers, designed and constructed a series of nest boxes—from quarter-sawn oak, no less—which will be monitored to prove, or disprove, the presence of the mice.
I’d suggest the company offer these for sale to the public as well at a premium, complete with the Rolls-Royce stamp, to provide yet more habitat and raise money for further conservation efforts. (I might also suggest they investigate something a bit more suitable than bungee cord to secure it to the tree.)
Terrain Tamer parabolic springs . . . a transformative modification
Can a leaf-sprung vehicle be endowed with the ride and compliance of a coil-sprung vehicle?
After installing a set of Terrain Tamer parabolic spring on our 1973 FJ40 Land Cruiser, I’d answer that question with: Close. Astonishingly close. Just one anecdote—when I first took Roseann for a ride after the installation, we’d not even got off our neighborhood byway onto a main street before she said, “Wow.”
First, if you’re not familiar with the concept, please read this, then this. But, briefly, a parabolic leaf spring is shaped in such a way that a single leaf can provide progressive resistance as it is compressed—it is, in essence, an extremely elongated parabola, thus its name. By comparison, the traditional standard leaf, stamped from flat bar stock, requires several additional, increasingly shorter leaves to provide progressive resistance, and those additional leaves produce substantial interleaf friction, reducing compliance and ride quality—especially in the case of a heavy-duty spring pack for a 4x4 vehicle, which might comprise eight, ten, or even more individual leaves. Theoretically a parabolic spring can be built with just a single leaf, but most systems use two or sometimes three, to provide backup in the event of one leaf breaking. But those leaves only contact each other at the very ends, via a thick anti-friction pad, so interleaf friction is nearly nonexistent. In fact, shocks for parabolic springs are valved more firmly to compensate for that reduced friction and the lack of self-dampening. Like a coil spring, a parabolic spring would continue to oscillate for some time after a bump if not damped.
Terrain Tamer has been making parabolic spring kits for Series Land Rovers, Hiluxes, and several other (mostly non-USA) vehicles for some time; not long ago they added applications for 40-series Land Cruisers, and offered to provide me with a set. The kit is exhaustively complete: four springs, four nitrogen-charged twin-tube shock absorbers, a steering damper, greasable anti-inversion shackles, and U-bolts. My kit also included TT’s own synthetic elastomer Pro bushings, which the company claims combine the vibration-absorbing properties of natural rubber with the durability of polyurethane. The bushings come with a specific molybdenum disulphide grease.
Terrain Tamer’s shock absorbers have an excellent reputation; however, I had an opportunity to try a set of Koni’s Heavy Track shocks. Koni’s Heavy Track Raid is the best expedition shock absorber I have ever used on overloaded Defender 110s in East Africa, so I jumped at the chance to install the slightly lighter-duty version on the 40.
Installation of everything was completely straightforward, with the additional benefit that the Konis are not nitrogen-charged and thus do not have to be forcibly compressed to fit them. Weighing the OME springs, then the parabolics, drove home one of the salient advantages of the latter: the swap removed 80 pounds from the Land Cruiser.
With it all bolted up, the Land Cruiser’s fender height was within a quarter inch of where it had been with the OME springs installed—the (to me) ideal 50mm/two-inch lift for an FJ40 intended for all-around use. Trying to suppress unrealistically high expectations—this is still after all a leaf-spring suspension—I headed out for a short drive.
I needn’t have suppressed any expectations. The ride was, in a word, transformed. One might demur by pointing out that the evicted OME springs were five years old, but I’d replaced and lubed their anti-friction pads not long before, and regularly greased the shackle bushings. No—this was a transformation. Harshness over minor irregularities in the road surface was simply gone, with the partial result that normal rattles and buzzes in the 40 seemed cut in half. Suspension action over larger holes and humps was astonishingly compliant.
I turned around and went back to the house to take Roseann for a ride, and she was just as impressed.
I let the suspension “settle” for a few weeks. From the side I then noticed a very slight droop at the rear—no more than a half inch, but I loathe a non-level vehicle. This was undoubtedly due to the substantial rear rack on the 40. So I installed a set of OME rear shackles, which are about an inch longer than the Terrain Tamer versions. “Problem” solved.
Stout Equipment rack (pre-parabolics)
A few days ago we took the 40 up into Redington Pass, east of Tucson. This route combines a severely degraded dirt road up the pass with several challenging 4x4 trails off it. The Terrain Tamer parabolics—along with the Konis—simply took 90 percent of the sting out of corrugations and potholes that were punishing with standard leaf springs. Once on the trail, the extra compliance was obvious, keeping all four tires in contact with the surface in spots where I typically lift a wheel. Impressive. Even in a video of a simple drive-by (see the Firestone M/T2 tire review) you can see how much easier the ride is.
Over my entire 40-plus-years ownership of the FJ40, no modification I’ve done has had anywhere near such a profound effect on the very nature of the vehicle. Obviously it will be some time before I can attest to the durability of these springs, but the technology has been around long enough to be well-proven. If you own a leaf-sprung Land Cruiser or Land Rover, I cannot recommend Terrain Tamer parabolic springs highly enough.
Hint: When using “Search,” if nothing comes up, reload the page, this usually works. Also, our “Comment” button is on strike thanks to Squarespace, which is proving to be difficult to use! Please email me with comments!
Overland Tech & Travel brings you in-depth overland equipment tests, reviews, news, travel tips, & stories from the best overlanding experts on the planet. Follow or subscribe (below) to keep up to date.
Have a question for Jonathan? Send him an email [click here].
SUBSCRIBE
CLICK HERE to subscribe to Jonathan’s email list; we send once or twice a month, usually Sunday morning for your weekend reading pleasure.
Overland Tech and Travel is curated by Jonathan Hanson, co-founder and former co-owner of the Overland Expo. Jonathan segued from a misspent youth almost directly into a misspent adulthood, cleverly sidestepping any chance of a normal career track or a secure retirement by becoming a freelance writer, working for Outside, National Geographic Adventure, and nearly two dozen other publications. He co-founded Overland Journal in 2007 and was its executive editor until 2011, when he left and sold his shares in the company. His travels encompass explorations on land and sea on six continents, by foot, bicycle, sea kayak, motorcycle, and four-wheel-drive vehicle. He has published a dozen books, several with his wife, Roseann Hanson, gaining several obscure non-cash awards along the way, and is the co-author of the fourth edition of Tom Sheppard's overlanding bible, the Vehicle-dependent Expedition Guide.