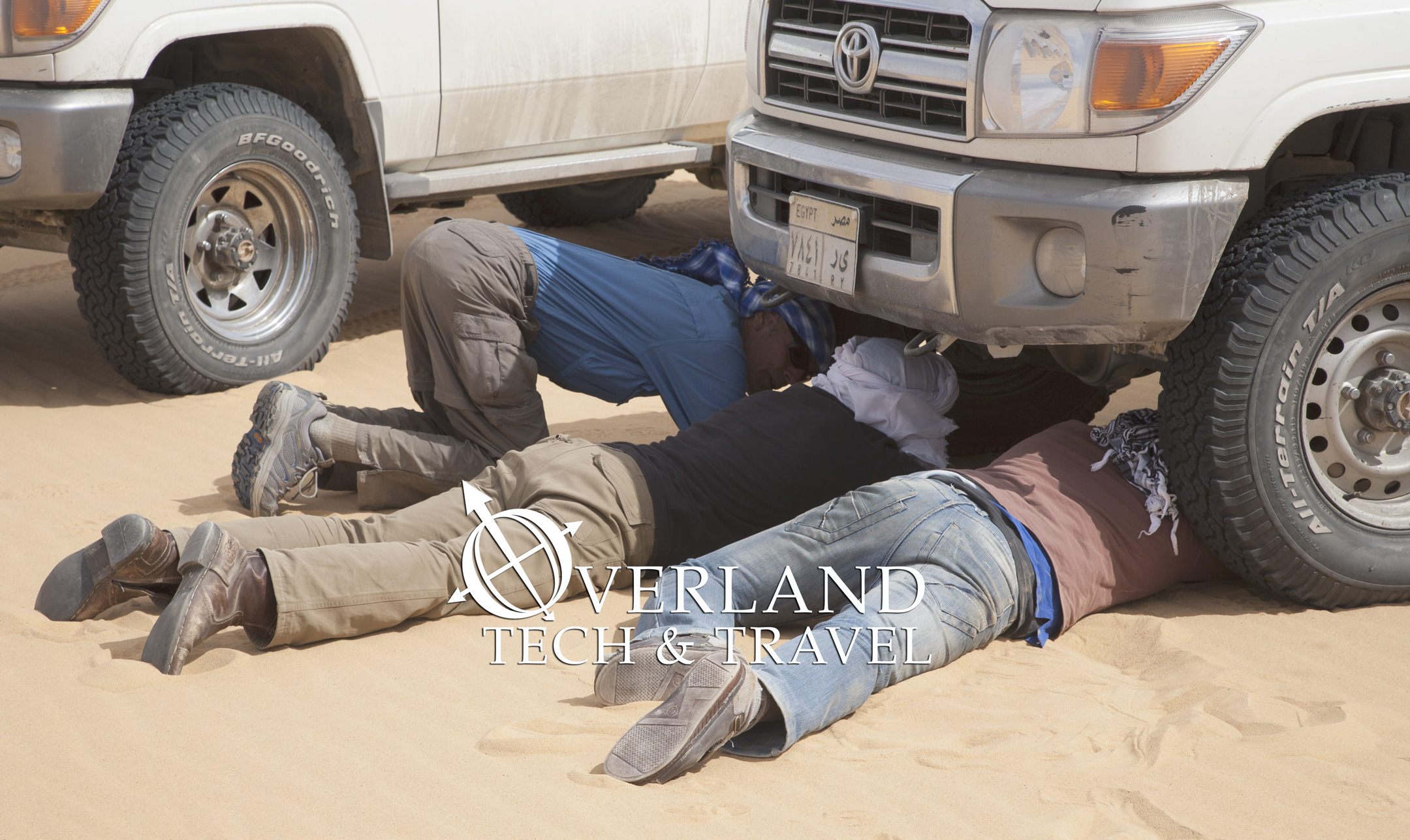
Overland Tech and Travel
Advice from the world's
most experienced overlanders
tests, reviews, opinion, and more
Life . . . and a trouble-free journey . . . is all about the details
Okay, no snickering about the technicolor assemblage above. The two jerry cans are colored appropriately for their purpose—blue and water, yellow for diesel. The tangerine gas bottle is courtesy Graham Jackson, who bought it and had it filled for us in Durban while we were still en route to Africa. Not sure if that was the only color available or if he was having some fun. And the straps? Green was all they had, okay?
But that’s not the story here. The story is about the level of detail one should aim for when inspecting a vehicle before a major trip, and especially the level of detail one should aim for when inspecting a new piece of equipment or a new accessory.
Consider this double jerry can and gas bottle carrier, custom-made to fit on the Kaymar rear bumper on our Land Cruiser Troopy. It seemed more than adequate when we picked up the vehicle after its installation. The pivot rides on a heavy-duty bearing and was rock-solid. I liked the locking bars to prevent fuel or water theft. I wasn’t pleased with the sharp edges of the tie-down strap keepers, but they seemed adequate until we got the Troopy back to the states where I could modify them. Our supplier had already installed a NATO fuel can and a plastic water can in it, so we simply filled them and left on the trip, which this time was a long, long route with no fuel resupply for at least 700 miles. And we had no trouble with the carrier.
The next trip, our last in Australia, involved another long no-resupply section (have you gathered these are common in Australia?). Although we had more than enough fuel under even the most pessimistic calculations, I nevertheless filled the yellow can on the rack.
A good ways along the Anne Beadell Highway, at the Ilkurlka Roadhouse, I walked around the back of the vehicle and smelled, then saw, diesel fuel pouring in a tiny but steady stream from the bottom of the can. When I pulled out the can and looked at the bottom of its receptacle, I immediately saw why. The base of the receptacle had been assembled in such a way that it left four welds protruding above the rest of the base. One of those welds had simply ground its way through the jerry can.
It was not an issue for that trip, but it could well have been on another with more critical fuel needs. People have, indeed, died from identical issues. While we were in convoy with friends, and had satellite telephones, it still could have presented a major hassle.
When we picked up the Troopy in Durban this week, I addressed the problem temporarily but effectively with a double layer of the yoga mat material we always carry for lining cabinets and stopping random rattles. With new jerry cans in place we were on our way.
It was a good lesson.
Secure—really secure—storage. Boss Strongbox
There are few things I enjoy more at the Expo than discovering high-quality products from makers unknown to me. At the West show, during a break between shepherding people around the General Tire driving track, I noticed some very handsome drawer systems at one booth. Closer inspection revealed them to be several steps above most similar products, with such stout construction and security features that they were more like safes that happened to have a drawer.
Indeed, talking with Ryan Curtis there, it developed that Boss Strongbox had been making vehicle storage systems for law enforcement departments and the military for a decade—generally to secure weapons—and only recently decided to address the overlanding market. The result is a selection of storage boxes and drawer units that go way beyond the usual “security” systems from most manufacturers.
My eye fell upon one of their smaller offerings, a versatile-looking pistol or camera-sized safe, mostly square but with a half-hexagonal front shape. Made from 16-gauge cold-rolled steel (like most of Boss’s offerings), it incorporated an overhanging lip on the lid, and an internal lip formed from a second layer of steel, making the lid double-thickness—and double pry-proof.
The lock was a substantial Medeco rather than a hardware-store bit, and the actual locking tab was a thick rotating steel piece that slid into a snug slot. With this box properly bolted down a thief would have a very difficult time breaking into it even with a good-sized crowbar. There’s simply no purchase or access for prying.
I have a large custom-made safe under the driver’s seat of the FJ40, but it’s a bit difficult to access quickly. I’ve often wished for a smaller (and stouter) safe for quick storage of the pistol I usually have with me, for when I need to visit a government building or other place where weapons are not permitted. This is it. I’m still pondering where to mount it, as over the years I’ve filled the Land Cruiser with platforms, built-in boxes, and a water tank. Since the Boss Strongbox takes up no more room than it needs for its mission, it shouldn’t be too difficult.
Boss makes other and larger safes, up to rifle length and with much more volume, along with a growing number of bespoke drawers systems. All are made in the U.S., all are finished in a durable crackle powdercoating, all are expensive, and all are worth every penny if you value what you plan to store in them—or if those items absolutely need to be kept out of the hands of potential criminals. Highly recommended.
Boss Strongbox is here.
KC Hilites roll bar clamp—a versatile multi-purpose mount
Years ago I was at a KC Hilites booth somewhere and the rep gave me one of their universal tube clamps, designed to mount driving lamps or other things to a roll bar or cage. I tossed it in a drawer and forgot about it—until recently, when I bought a rechargeable Streamlight Stinger flashlight to be dedicated to the FJ40.
Since the tube clamp is plastic it was easy to drill it to mount the flashlight’s charger base to it with stainless 3/16th bolts and nylock nuts. I mounted the assembly to the roll cage above the passenger seat, where it is out of the way but accessible to either passenger or driver. I ran the power cord down the vertical tube of the cage to the 12V socket I installed in the dash there a few years ago (above a DIN socket).
The KC tube clamps are available in various sizes, to fit tubes from .75 to three inches. The possibilities for uses are endless.
Find them here.
Warn's 70th anniversary M8274-70 winch
Warn’s venerable 8274 winch is one of two—the other being the Superwinch Husky—that could legitimately claim to be the best electric winch on the planet.
Each has its advantages. The Husky’s worm drive means it needs no external braking system; it is fully controlled whether powering in or out. The 8274’s spur drive gear train does require a brake but is significantly more efficient (about 75 percent versus 40 percent). It’s more a personal (or patriotic—British versus American) choice rather than a which-one-is-better decision.
Now, to celebrate the company’s 70th anniversary, Warn has announced a limited-edition, uprated version of the 8,000-pound-rated M8274-50. Only 999 will be available world-wide, at an eye-opening retail price of $3,100 (although $2,500 seems to be the going street price). The commemorative M8274-70 is rated to a full 10,000 pounds, and includes 150 feet of 3/8” synthetic line, a solid-state, waterproof Albright contactor rather than a solenoid, plus a few odds and ends such as uprated bearings, a stainless steel spool knob, and a billet aluminum hawse fairlead. (Warn’s site also notes that the winch’s box “features commemorative packaging.”)
I’ve had an 8274 on my FJ40 for about ten years now, and it has performed flawlessly both in the field and through many training sessions. So I delved into the new one to see what had changed besides the extra power (courtesy of a series-wound six-horsepower motor rather than the 4.6 hp version in mine).
And immediately this caught my eye:
“Up to 50% faster line speed at rated load vs. previous M8274-50.”
Fifty percent faster? One of my only complaints about the M8274-50 is that it is too fast already. Speeding it up even more is the last thing this winch needs.
Winching, more than any other recovery technique, is fraught with the potential for errors that could have disastrous consequences if the operator is not properly trained, paying one hundred percent attention, and ensuring that every step of the procedure is conducted in a controlled manner. The best way to guarantee a safe and successful winch recovery is to go slowly. The only exceptions I can think of to this rule are if you have stupidly bogged your vehicle below high tide line with an incoming tide, or have gotten stuck in the middle of a fast-flowing river that is scouring substrate out from under your tires and sinking the vehicle farther. Otherwise my opinion is that it is impossible to have a winch that is too slow. Indeed, on most recoveries or lessons with my 8274 I rig a double-line pull out of habit, just to ease the pace (since a double-line pull halves line speed while doubling power). I can’t imagine it 50 percent faster.
I wonder if the impetus behind this drive for faster line speed comes from a misdirected emulation of competition events such as King of the Hammers, where winches are commonly modified to achieve outrageous line speeds. Suffice to say that for overland travel, you do not want to use competition rock buggies as your build inspiration.
This in no way (well, barely) diminishes my respect for Warn’s 8274 series winches. The new one would be a fine choice for a heavier expedition vehicle in the 7,000-8,000-pound range. But I’d suggest employing a pulley for most recoveries—unless shark fins are circling offshore or trout are showing up in the footwells.
The new ARB Elements fridge/freezer
The call came from our commercial mail service. “Hi Jonathan. You have a really big box here, and it’s heavy!” I knew it could only be one thing: the new ARB Elements fridge I’d been assigned to review for OutdoorX4 magazine.
Even back home and excised from its substantial packing, the Elements fridge is an impressive piece of equipment at 70 pounds, 32 inches long, 19 inches wide, and 17 high. It’s strikingly handsome as well in its cladding of 304 stainless steel and black trim. You might or might not go for the huge embossed ARB logo on each side, but the formed panel increases rigidity so it’s not purely cosmetic.
More important is the substantial redesign—a complete re-envisioning, actually—that ARB undertook three years ago when conceptual work reportedly started on this fridge. In an increasingly crowded and sophisticated market, a simple tweaking of the previous model, introduced in 2008, wasn’t going to cut it. So the Elements (available for now only in a large 60-liter version) incorporates a bunch of innovative features.
First, as the name implies, is the weatherproofing. You can leave this fridge strapped down in the bed of your pickup all year (preferably using the available tamperproof bolts). Precipitation won’t hurt it, and the black ASA (acrylic-styrene-acrylonitrile) trim is similar in strength to ABS resin but significantly more resistant to UV degradation. The hinges are stainless-steel castings; the twin aluminum latches are a huge improvement over the previous generation’s single plastic catch, which always felt fragile. (However, one disadvantage compared to the old fridge is that there is no easy way to quickly strap this one down without purchasing the optional tie-down kit or mounting base. The carry handles are comfortable but provide no way to loop anything over them.)
The three icon buttons lower left control the electronic combination lock
There’s a slot to secure a padlock, but a far more stylish way to prevent your friends pilfering your Samuel Smith’s ale is the electronic lock incorporated into the (weatherproof) control panel. Program in your own code using the three icon buttons, or leave it disabled as you wish. With the lid locked closed, the recessed temperature buttons cannot be accessed, so your stymied and jealous friends can’t secretly warm up the beer. The lock projects a pin into a fitting in the lid, and would clearly not withstand a crowbar, so if serious antitheft capability is needed (i.e. steaks, lobster, Veuve Clicquot, etc.) I’d default to a shackled lock.
Open the lid and the first thing you’ll notice is the clever single hydraulic strut, which magically holds the lid open at any position you wish. An LED lights up the all-white interior, which is massive if you’re used to the standard 40-liter-size fridge. There’s a big bottom compartment and a high shelf, which can be blocked off as a produce shelf by turning the basket around so its high side is toward the shelf. Turned the other way, the basket allows long items to be laid horizontally. One feature that might be an issue for some vehicles: There is no way to convert the lid to side-opening.
Mechanically, the Elements uses an industry-standard Nidec/Secop (formerly Danfoss) BD35F compressor, with a three-stage low-voltage cutoff. Of the two standard 12V fridge compressors—this and the Sawafuji swing-motor compressor—the Secop tends to run more quietly at the expense of a more complex mechanism. The Secop can also be run at different speeds to optimize power use. Both compressors have proven reliable over the years, and both will operate at significant angles, unlike the cheap absorption-type fridges still found in some RVs and campers. ARB enhanced the performance and efficiency of the Elements by incorporating a full-height evaporator; this should keep temperatures more uniform throughout the fridge. Those temperatures can be dialed down to 0º Fahrenheit (-18ºC) if you choose, even in 90º (35ºC) weather. The walls on the Elements are noticeably thicker than those on my old ARB fridge, which will also help keep power consumption down.
Options for the Elements include a remote temperature monitor, various bases, and a tie-down kit. If you buy the latter, a word of caution: The slots on the metal buckles of mine were razor sharp and would have severed a strap in short order; I had to file them smooth.
I was a bit surprised that ARB’s initial release of the Elements was in the larger, 60-liter model rather than the more common 40-45-liter size, but perhaps the decision was driven by their own sales figures of the previous version. I’m certain other sizes will follow, and I’m curious if the company will eventually add a model with separate fridge and freezer compartments.
Overall, I think ARB has built a fridge that is several genuine steps forward and will carry on the sterling reputation of the company.
Measure first! The Elements barely fit in the back of my FJ40
ARB USA is here. Retail on the Elements fridge, for some strange reason known only to the marketing department, is $1444.49
New MAXTRAX Xtreme
It’s well-known that I’m a fan of the original MaxTrax, and have defended them against cut-price copies. I’ve also noted that I refuse to use the company’s all-caps MAXTRAX spelling, which as a grammarian I find wincingly annoying (I compromise with MaxTrax). Now . . . sigh . . . the company is torturing me again with their new product, named the Xtreme. Ugh.
I grit my teeth and continue, because the new product, a prototype of which I received recently, looks to be a significant leap in the technology of composite recovery mats. Why? Because the teeth, or studs, of the new mat are made from hard-coated aluminum rather than molded-in nylon. And . . . they are user-replaceable.
As anyone who has used them knows, the salient disadvantage of composite recovery mats is that, if you allow too much wheel spin while attempting to climb onto them, the studs can melt, significantly and permanently reducing the effectiveness of the product. Recent mats using harder plastic studs helped but did not cure the issue. The Xtreme might just do so.
The composite base of the new mat is the same reinforced nylon material as the original MaxTrax, which I and many other testers have found to be superior to the polyethylene used by some lower-priced competitors. There is also extra reinforcement in the bottom webbing. Combining that with the aluminum studs should provide vastly improved durability.
As you might expect, the Xtreme is a bit heavier than the standard MaxTrax—8.9 versus 7.4 pounds each. But at 18 pounds per pair that’s still lighter than even perforated aluminum sand mats.
They are not, however, cheaper. Retail on the Xtreme will be $449 a pair. I remember being scandalized at the idea of the original $300 MaxTrax—until I used them. I suspect our perspectives will continue to evolve as long as such price increases are backed up by such meaningful improvements.
A better Hi-Lift base plate.
Let’s be honest: You can make a perfectly functional base plate for a Hi-Lift jack by gluing together a couple of foot-square pieces of 3/4-inch plywood. If you want to get fancy you can add a third layer of 1/2-inch plywood with a cutout for the jack’s foot, to help stabilize it. This is exactly what I used for years.
However, the plywood got chewed up pretty quickly, and once I used it in mud it started delaminating. So I switched to one of the ubiquitous red plastic bases. It was (and is) an excellent product, and mine has held up through not only personal use but numerous training classes as well.
My only real issue with the red base is its bulk, which is significant if you’re storing it in the back of an FJ40. It takes up an inordinate amount of volume for a single-function implement.
While shopping for some items we needed for Expo East this November at one of the Tractor Supply Company (TSC) stores, I chanced upon a solution in the form of the Reese Farm Jack Foot Plate. Constructed of thick polypropylene, it’s far more compact than the red base, yet boasts a 7,000-pound capacity. I put it to an unusual but effective trial at the show: Our 20-foot cargo trailer, which hauls all the Expo equipment and grosses about 10,000 pounds, had to be parked where the tongue jack would be in very soft mud. So I placed the Reese plate under the tongue’s foot, lowered probably 2,500-pounds plus onto it—and left it there for the duration of the show. It emerged unscathed and unwarped.
The Reese plate is one-third the height of the red base but seemes even thinner, it’s so easy to stash. And I like the low-profile black color, too. This is my new standard-equipment Hi-Lift base plate. About $25 from TSC or Amazon.
Quality, seen and unseen
For several years I’ve stored my “in-town” automotive tools in a modest older Snap-on rolling chest combination (which I bought used). But it’s been getting really crowded recently, and I’ve been thinking about augmenting or replacing it. The decade-old Craftsman chest out at our desert place is larger, but I didn’t want to just swap the two as I still need a full complement of tools out there as well.
By sheer coincidence I was at an acquaintance’s house last week to deliver a gate opener I’d sold him, and it turned out he had recently bought the entire remnant stock of Kobalt tool chests from the local Lowe’s home improvement stores. Kobalt had been the chain’s store brand for years, but recently they switched to Craftsman—which, as you might know, is now owned by Stanley Black and Decker rather than Sears. In my mind this switch is actually a step down: Recent made-in-China Craftsman tools that I’ve examined in their packaging show noticeably poorer finish than the older made-in-America products, poorer in fact than the few Kobalt tools I’ve purchased to review.
Anyway, my friend had scored several dozen of Kobalt’s top-of-the-line stainless-steel-clad tool chests, and quickly unloaded all of them at fire sale prices. He had exactly one left, and it happened to be a tall, narrow, 27-inch-wide model, which is the only configuration that will fit in the in-town garage. So I bought it for a song.
Back at home I had to pull the drawers to unload it and get it into position. And that gave me the opportunity to look past the beautiful stainless exterior and the nifty soft-close drawers. What I noticed made me pull apart that plain old red Snap-on chest to examine it as well. And that’s where significant differences showed up. Drawers out, the Snap-on cabinet was noticeably heavier and more torsionally rigid than the top box on the Kobalt. Where Snap-on used nuts and bolts and spot welds to assemble pieces, the Kobalt had been assembled almost exclusively with pop rivets—in fact I found several stems from those rivets still inside the cabinet. Both brands incorporate smooth roller-bearing drawers, but when I re-installed the Snap-on drawers they each slotted perfectly into their slides and snicked home effortlessly, while the Kobalt’s drawers proved to be a real pain to get properly lined up. I had to carefully fit each side in each slide to prevent it simply falling out, then guide the assembly in until it clicked back together—after which, I should note, each worked perfectly, including the soft-close function.
Don’t get me wrong: The Kobalt chest is a very nice item and I’m glad I bought it, especially at the price. I’m sure it will serve my amateur mechanic needs adequately, as I’m only in those drawers a dozen times per month, rather than dozens of times per day as a pro would be. But it was clear that the Snap-on chest would hold up to that kind of use far better than the Kobalt would. (And I managed to squeeze the Snap-on chest into another corner of the garage.) Snap-on certainly puts a hefty price premium on its products, and it is inarguable that a good part of that premium is strictly due to the name and cachet, but at least you get the excess you pay for.
In a larger context, it points out the obvious fact that external looks aren’t everything. It’s the engineering underneath that determines quality.
Hint: When using “Search,” if nothing comes up, reload the page, this usually works. Also, our “Comment” button is on strike thanks to Squarespace, which is proving to be difficult to use! Please email me with comments!
Overland Tech & Travel brings you in-depth overland equipment tests, reviews, news, travel tips, & stories from the best overlanding experts on the planet. Follow or subscribe (below) to keep up to date.
Have a question for Jonathan? Send him an email [click here].
SUBSCRIBE
CLICK HERE to subscribe to Jonathan’s email list; we send once or twice a month, usually Sunday morning for your weekend reading pleasure.
Overland Tech and Travel is curated by Jonathan Hanson, co-founder and former co-owner of the Overland Expo. Jonathan segued from a misspent youth almost directly into a misspent adulthood, cleverly sidestepping any chance of a normal career track or a secure retirement by becoming a freelance writer, working for Outside, National Geographic Adventure, and nearly two dozen other publications. He co-founded Overland Journal in 2007 and was its executive editor until 2011, when he left and sold his shares in the company. His travels encompass explorations on land and sea on six continents, by foot, bicycle, sea kayak, motorcycle, and four-wheel-drive vehicle. He has published a dozen books, several with his wife, Roseann Hanson, gaining several obscure non-cash awards along the way, and is the co-author of the fourth edition of Tom Sheppard's overlanding bible, the Vehicle-dependent Expedition Guide.